Introduction:
Bus operations are complex, and so is scheduling. It is a combination of craft and science, and transportation operators devote considerable energy to getting vehicle and crew scheduling (aka blocking and runcutting) right. They do this to ensure efficient operations, cost savings, on-time performance and regulatory (and labor rule) compliance.
Yet, the same amount of energy isn’t always applied to rostering. In fact, 71% of US agencies surveyed by Optibus did not use roster optimization. Historically, the industry has focused on using optimization during the scheduling phase and less so during the rostering phase. Now, as technology advances, it is time to look at rostering, especially since it impacts costs, driver satisfaction and safety. This ebook will explain why and how.
What is rostering?
Rostering is the last optimization step. First come route planning and timetables. Then vehicle and crew scheduling (blocking and runcutting) as well as relief vehicle scheduling. Rosters are last.
Rostering is the process of grouping daily operator runs (shifts or duties) into packages of weekly work assignments. These assignments are typically five eight-hour runs or ten four-hour runs. They may include a combination of different runs such as: weekdays only, weekdays and Sunday/Saturday, and other combinations.
Rostering can be done in several methods. They include manual rostering by schedulers; “cafeteria-style rostering” in which drivers build their own rosters by picking which runs and days off they want; and the use of roster optimization algorithms through a planning and scheduling platform.
Of all three methods, only roster optimization uses technology rather than human input to ensure the creation of the most high-quality rosters while reducing overtime costs, adhering to break rules and rest time, and implementing driver preferences (for instance, regarding split shifts or start times).
Why is roster optimization important?
Overtime pay and guaranteed pay:
Since (in most cases) overtime is determined on a weekly basis, rosters are the only way to control overtime costs, which can represent 2-5% of all labor-related costs. Reducing the ratio of overtime to total paid time can offer significant savings. Similarly, when drivers are guaranteed pay if they work less than a minimum amount of hours, roster optimization can be used to ensure they work these hours rather than be paid for guaranteed time. Roster optimization does what the human cannot: even out duties into packages that will contain the right amount of weekly hours for all drivers, without having too many drivers that get too many or too few hours.
Fairness and delivering quality rosters for drivers:
The ability to spread duties in a way that will provide good outcomes for all drivers, instead of the lucky few that got overtime or a full 40-hour-a-week roster, provides a fairer outcome for drivers. Fairness is an important source of emotional satisfaction at work, and can help retain drivers and even provide hiring incentives. Roster optimization means there are many good options for many drivers, ensuring more drivers are happy with their roster assignments and overtime is allocated only when needed.
Some agencies allow their operators the convenience of “cafeteria-style rostering,” meaning operators can pick their schedules. They get to pick their shifts a day at a time, and those shifts add up to a roster. Normally the order of picking is based on seniority. Many times cafeteria style-rostering creates a duty allocation that is not equitable nor efficient.
Reducing the roster count:
In some cases, optimized rostering can reduce the roster count, meaning that fewer drivers are needed to cover the same routes. This can be helpful in times of driver shortages and can save costs. Schedulers can constrain roster counts as part of a what-if scenario to see whether they are better off with more rosters and less overtime, or whether overtime with a reduced roster count is better.
Compliance and safety:
Roster optimization makes it easy to comply with labor laws, union agreements and safety requirements such as rest time between duties and breaks during duties. This ensures all rosters are compliant and valid and saves valuable scheduling time.
Dealing with different driver groups:
In case the transportation organization has different drivers to whom different labor rules apply, roster optimization is sometimes the only effective way to make sure the organization is complying with the rules for each group, and such optimization can produce valuable savings.
Creating rosters
Three key components factor into creating a viable roster:
Compliance with regulations & collective bargaining agreements (CBAs)
CBAs and other regulations determine the minimum/maximum weekly (or period) hours, number of workdays, time off requirements, break regulations, etc. All these rules and preferences (for instance, at least two consecutive days off) need to be reflected in the roster or schedule.
Safety requirements
Safety is crucial when creating a roster; making sure drivers get enough rest before their shift and that shifts are spaced correctly can be an important safety requirement. Other requirements relate to duration of duties, start and end times, length of the duties prior to a break, etc. In some countries, transportation regulators are attempting to create fatigue indices to model fatigue and ensure operators can drive safely.
Driver satisfaction
Roster optimization isn’t just about ensuring savings on overtime and guaranteed time. Rosters are an incomparable opportunity to improve drivers’ work-life balance. This can be anything from route familiarity, similar start time and end times, and rosters that are designed for specific groups, such as retirees with a part-time job or single parents. Think of this as a way of aggregating driver preferences (morning shift/late shift, start times, routes, etc.) and taking them into consideration to create as many quality roster packages as are required. This can help deal with driver shortages, prevent burnout and offer good conditions for new drivers that join. Before you begin rostering, make sure to interview drivers and check with them what is a good roster from their point of view.
Roster optimization in practice
Here are some practices that advanced scheduling platforms offer schedulers to help them create better rosters.
Comparing roster scenarios
In scheduling, there is a simple truth: more scenarios equal better results. Using quick and powerful optimization can assist in creating many roster scenarios quickly. This enables a better understanding of the trade-offs associated with different roster rules.
Here are four KPIs you should pay attention to in each scenario:
- Overtime
- Make up (guaranteed) time
- Pay hours
- Number of rosters
Four or five-day workweek
Probably the first thing to check is the impact of a four-day workweek with 10 hours a day, a five-day workweek with eight hours a day, and a mixture of the two. This can be easily defined in the roster rules and preferences settings, and scenarios can be prepared to check the options and their impact on business KPIs. Additionally, different “roster groups” can be created with some drivers in the 4-day workweek group and some in the five-day workweek group.
Consecutive days off
One of the greatest benefits for drivers, regardless of which work week they have, is to make sure that days off are consecutive, so that their time off works well for them. Additionally, you can use roster optimization to put short shifts (if they exist) just before days off, so that the time off is long and uninterrupted.
Start times and route variation
The following example is a scenario focused on overtime cost reduction. This looks like a successful optimization: The result is zero overtime, meaning in this case that about 1,500 hours are saved annually. Yet, this is no success if the rosters are of low quality for drivers.
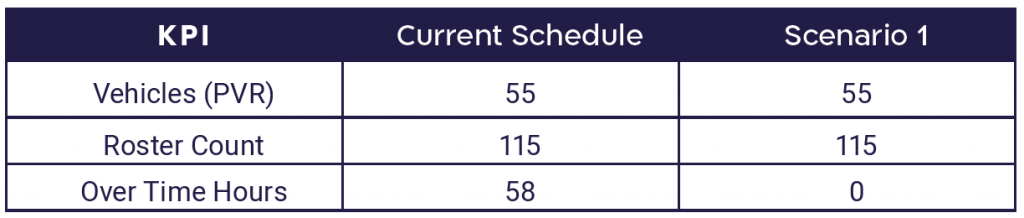
In this case, low quality can be related to two issues: too many routes per roster or a large variation in different start times for each day, which can be a problem for drivers. This can be addressed by modifying the roster preferences, such as requiring similar start times or limiting route variation. This is also an example of where scenario analysis can help, because we can test several requirements for route homogeneity and see which works best.
Evaluating different scenarios
Take a look at the following scenarios. Each one of them has a different goal. One is focused on zero overtime, another on reducing the number of rosters, and the third on start time similarity.
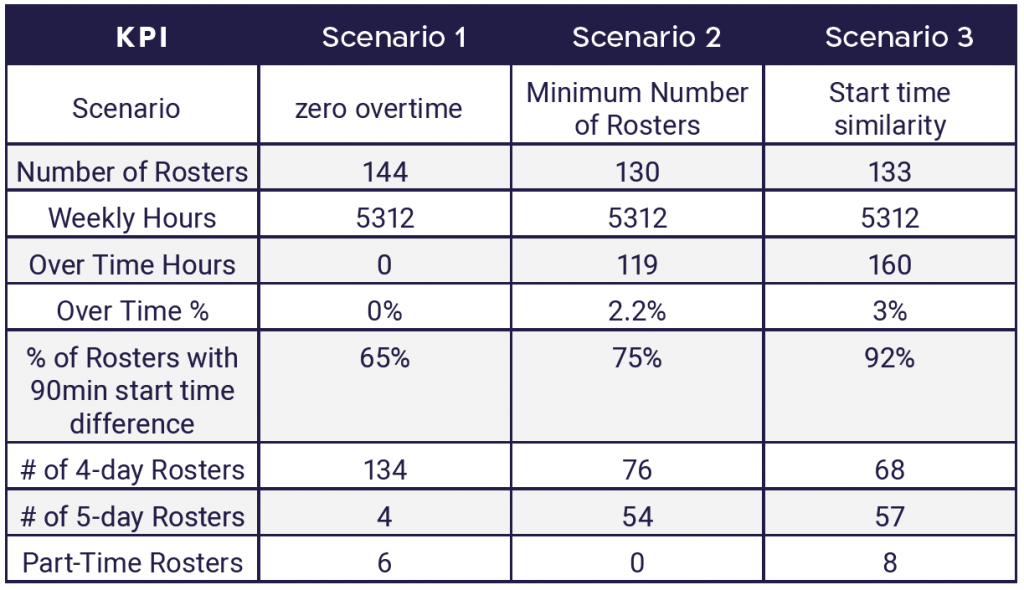
Scenario 1 does not allow overtime, but the trade-off is that only 65% of the rosters have a similar start time, meaning that there is no overtime, but perhaps the overall roster quality is lower, from the drivers’ point of view.
Scenario 2 focuses on reducing the number of rosters, reducing roster count by 14. Yet it adds 119 overtime hours, which may still be plausible given that overtime here is perhaps required to deal with driver shortages.
Scenario 3 focuses on enabling drivers to start their shifts at a similar time each working day. Here, the trade-off was a 3% overtime increase, adding 41 overtime hours.
Roster groups
Roster groups enable the creation of different types of rosters for different groups
of drivers (for example, new drivers vs. veteran drivers). Veteran drivers may enjoy
rosters that suit their preferences (reflecting their tenure). It may make sense
to create different groups for part-time drivers and full-time drivers or create
different groups for drivers with a four-day workweek and drivers with a five-day
workweek, or different groups for drivers to whom different union rules apply.
Using advanced scheduling platforms allows schedulers to easily input different
driver preferences and cater to a variety of driver needs within the specific roster
group, while ensuring optimized results for each group separately and across the
different groups.
Rotating Rosters
Rotating rosters mean rotating duties between the different members of the roster. A simplified example of such a roster would be a rotating roster with 3 drivers: Tim, Jane and Bob. Tim is assigned roster line 1, Jane is assigned roster line 2 and Bob is assigned roster line 3. Since each driver moves on to the next roster line after each is completed, the next week Tim would get roster line 2, Jane would get roster line 3 and Bob would get roster line 1.
There are two key benefits to rotating rosters.
1. Equitable duty allocation for drivers
Assuming roster line 1 is the most preferred, only one driver gets it and the rest have to do without it. In rotating rosters all drivers in the group will get the preferred roster lines at least some of the time.
The roster lines for a given set of drivers can be similar (for instance, they can have roughly the same start time), or operators can cycle through alternating roster lines (for instance, an early week followed by a late week). Either way, drivers with rotating rosters benefit from knowing what their week will look like far in advance, allowing them to make personal plans around their working hours.
In addition, some operators say they prefer taking on the diversity of tasks that may be available with a rotating roster because it makes their work more interesting.
2. Maintenance becomes easier
Since all the operators within the group are familiar with all the duties, It is easier for operators to cover for each other if someone is sick or running late. This duty familiarity makes it easier for dispatchers as well. With rotating rosters, drivers can still get “good” roster lines, while schedulers don’t have to work hard on tailoring them to specific drivers.
Validations
Last but not least, advanced platforms offer schedulers the benefits of using the power of algorithms to validate the rosters and make sure they comply with all necessary labor agreements or alert the scheduler about any violations.
When a non-rotating roster is optimized, each of the rules is validated within a given roster line, since operators perform the same duties each week. When rotating rosters are optimized, the validations take the adjacent roster line into account as well, since drivers switch duties from one roster line to the next.
In some cases, duties that are valid when looking at one roster line at a time are invalid when evaluated in the context of a rotating roster and vice versa due to the driver change that happens in a rotating roster.
Summary
It’s time that the technology allowing roster optimization be put into practice. Roster optimization is a win-win for all involved. It saves time for schedulers, freeing them to focus on passenger satisfaction; it offers better conditions for drivers, ensures compliance with regulations and union rules, and saves money.