When we talk about scheduling optimization, we often focus on vehicles and drivers and forget an important factor: relief vehicles. Relief vehicle scheduling is about how to move drivers between “pieces of work” – the trips each driver is responsible for. For example, if a driver’s shift doesn’t begin at the depot, they need a way to get to the bus they’re driving. If they have a changeover during their shift, they need to get to the second bus they need to take over. If their shift ends downtown, they need to get back to the depot, where they began their workday. Relief vehicle scheduling matters: finding efficient ways to move drivers enables us to best utilize driver time by allowing more ways to combine “pieces of work” as well as reduce deadheads and better implement interlining.
Schedulers have a number of ways they can choose to move drivers between trips:
- Walking
- Shuttles – Using existing transportation like buses or subways as a passenger.
- Relief Vehicles – Vehicles operated by the transit provider, and usually by the drivers themselves, used solely to transport drivers.
- Buses – In some cases, buses, while not in use, can be used to transport drivers (this is similar to a deadhead).
Relief Vehicle Scheduling Complexity
Schedulers must plan relief schedules under the obvious constraint of capital expenditure, which dictates the number of relief vehicles an agency can buy. Costs aren’t limited to only the purchase of these vehicles, but their operation as well.
But schedulers are constrained by more than just vehicle supply, as the best relief mode for each relief trip is dependent on that of the other trips — in other words, everything is interconnected. We can see where this can become problematic:
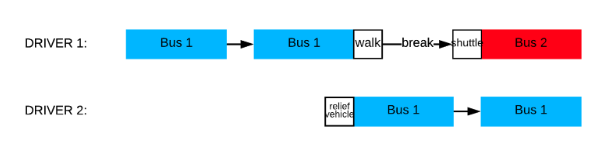
In the above graphic, two drivers are each responsible for a series of trips. Their relief modes are chosen purely based on what is best for that relief trip, without consideration of the other relief trips.
When Driver 2 takes a relief vehicle to take Bus 1, that relief vehicle is left unused because Driver 1’s first relief mode is walking. This is problematic for 3 reasons:
- Parking the relief vehicle requires parking infrastructure. It can also be time consuming, and possibly expensive. There may not even be a parking option in the relief location.
- That relief vehicle is out-of-service until the next driver picks it up, possibly increasing the total number of relief vehicles needed to operate the schedule and increasing costs.
- The relief vehicle needs to be returned to the depot at the end of the day and may not even be allowed to be left unattended in the relief location, so an additional relief trip must be planned to return the vehicle to the depot, further increasing costs.
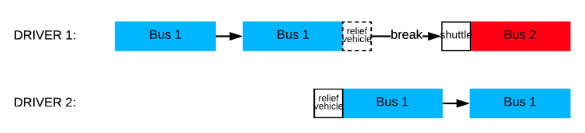
Now, Driver 1 takes the relief vehicle from Driver 2, and once he reaches his break location, he can pass that vehicle off to another driver. Creating these “chains” of relief vehicle use are necessary to maximize operational efficiency.
Optimization for Minimized Operational Costs
In this example, planning a relief vehicle chain of two drivers is easy. But, in a more realistic scenario, with a system of over a hundred drivers, creating these chains by hand becomes a lot more complicated and time consuming. Finding the optimal allocation of relief vehicles by hand is impossible. As a result of suboptimal relief vehicle allocation, many transit agencies employ more relief vehicles than necessary and, as a result, have less efficient duties due because less combinations were checked.
Optimizing relief trips with the help of software can enable us to uncover and realize operational savings. Not only can optimization tools identify the most efficient ways to pair and even chain relief trips and decide relief modes, they can simultaneously optimize runcuts and relief vehicles. Because relief vehicle scheduling, is, by definition, dependent on crew schedules, optimizing duties to enable efficient relief vehicle use and accommodate agency specific constraints (driver break requirements, available relief modes, etc.) can drastically impact operational costs, sometimes decreasing the number of vehicles needed to operate a relief schedule by up to 30%.
Simultaneous runcut and relief optimization produces operational savings in two ways:
- Driver’s breaks can be varied to reduce the amount of relief vehicles needed at any given time. Additionally, this allows better pairing options and the ability to create longer chains of relief trips, decreasing the need for vehicles.
- Relief trips that occur at the same time can be grouped by location, allowing drivers to share relief vehicles and decreasing the number of relief vehicles needed at any given time. Grouping also reduces the need to find pairing options, as drivers can be dropped off at their destination without having to hand off the vehicle (there is still someone to drive).
Enabling Holistic Analysis
While relief vehicle scheduling may not seem as integral as blocking or runcutting, it is an essential part of an efficient transit system. Ultimately, optimization tools allow agencies to approach scheduling more holistically by modeling every aspect of their transit system and finding the most efficient vehicle, driver, and relief vehicle schedules based on agency-specific needs. Not only can optimizing relief vehicles reduce operational costs and prevent excessive relief vehicle purchases, it produces time savings by relieving schedulers of the need to manually schedule relief vehicles following runcut optimization. This allows schedulers to use their time where it can be most impactful – fine-tuning schedules to better meet the needs of their agency and provide a better service for their customers.